For an OHS technician, organization is key for keeping workers healthy in their environment. That’s why the 5S method could be a total game changer.
An Introduction to the 5S Method for Health and Safety
The 5S’s refer to five Japanese words that provide the framework for the method:
Seiri: Sort – Remove unnecessary items from the workplace. Get rid of clutter and garbage that has accumulated.
Seiton: Set in Order – Arrange essential items in a logical, efficient layout for easy access. A place for everything and everything is in its place.
Seiso: Shine – Clean and inspect the work area. Cleanliness allows you to notice any potential hazards or issues.
Seiketsu: Standarise – Establish routines and procedures to consistently follow the first 3 S’s. This makes 5S a habit and part of the daily workflow.
Shitsuke: Sustain – Implement regular audits and checks to ensure 5S standards are maintained. Provide necessary training and positive reinforcement to sustain motivation.
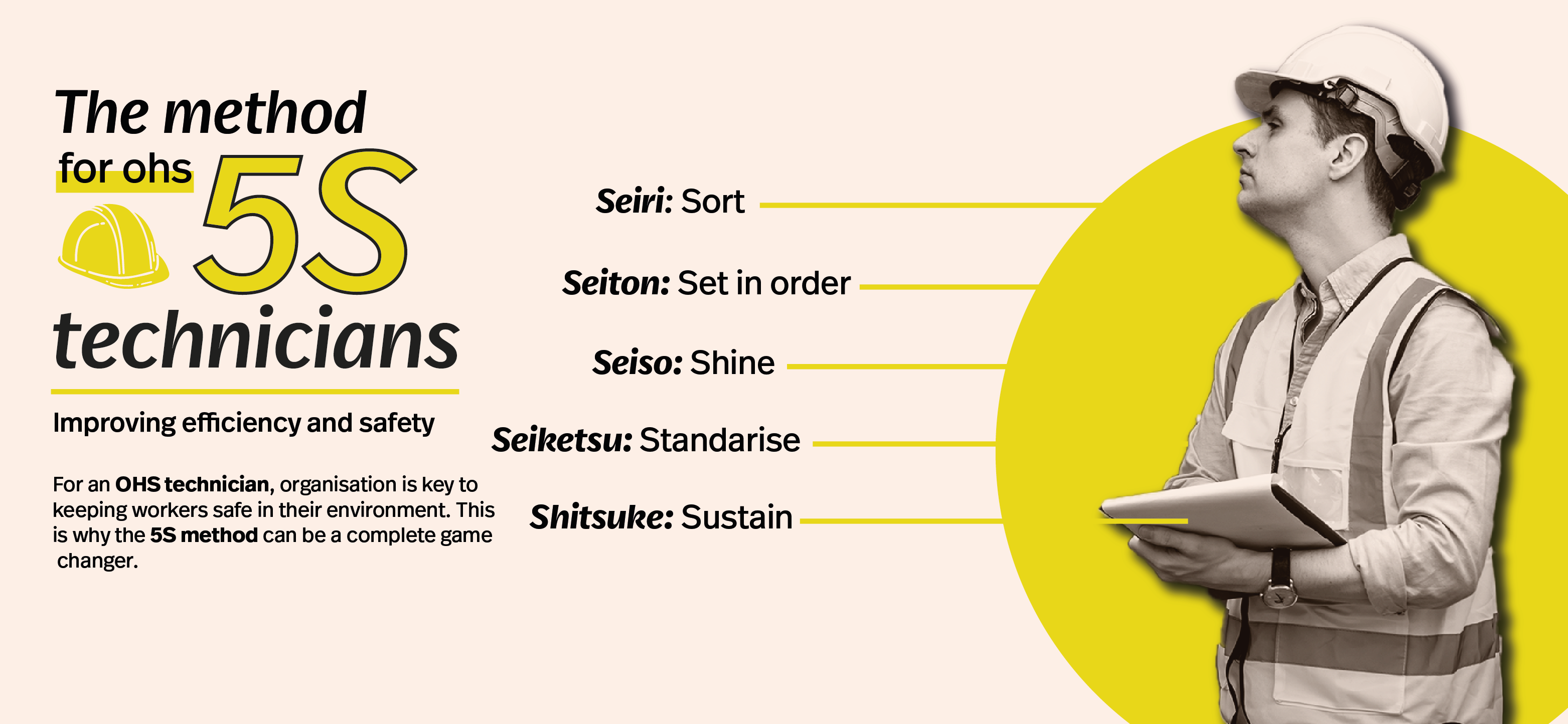
What are the benefits of the 5S and how it improves workplace safety?
Implementing 5S creates an organised, uncluttered workspace that makes it far easier and safer for OHS technicians to navigate the work environment, locate what they need, and spot any potential hazards. The routine inspections and audits also aid in identifying unsafe conditions before occurring.
Overall, this method enhances workplace organisation, safety, and productivity. For health and safety professionals, it provides a simple framework to systematically improve efficiency and reduce risks in their daily work.
Applying the 5S methodology to reduce workload
To help OHS technicians feel less workload while maintaining safety standards, the 5S methodology can be applied in the following way, emphasizing efficiency and workload reduction:
Sort:
• Review and prioritise OHS tasks and responsibilities based on their criticality and frequency.
• Identify and eliminate redundant or low-priority tasks that do not significantly contribute to safety objectives.
• Streamline and consolidate documentation and reporting requirements to reduce paperwork and administrative burden.
Set in order:
• Organise workstations and tools used by OHS technicians for maximum efficiency.
• Create a centralised and easily accessible digital database or physical repository for safety documents and resources.
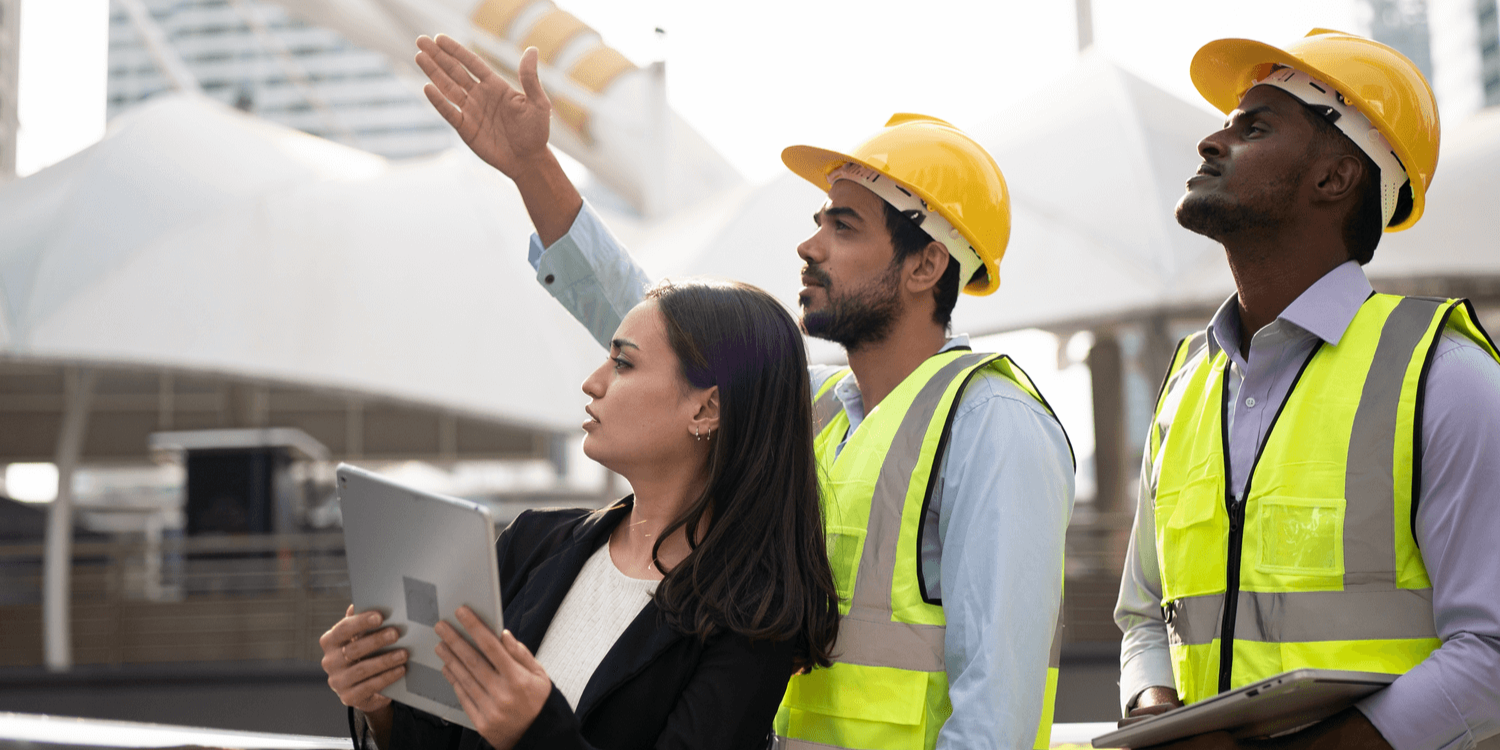
Shine:
• Regularly maintain and inspect safety equipment and tools to minimise breakdowns and unplanned maintenance work.
• Conduct safety audits and inspections with a focus on identifying potential hazards and addressing them proactively to reduce future workload associated with incidents and accidents.
Standardise:
• Develop standardised processes and workflows for common OHS tasks.
• Ensure that all OHS technicians are trained and competent in these standardized procedures to avoid variations in work practices.
• Implement digital tools or software to streamline data collection, analysis, and reporting, reducing manual data entry and duplication of effort.
Sustain:
• Foster a culture of continuous improvement and employee involvement in identifying ways to reduce workload.
• Regularly review and update standardized procedures to incorporate feedback and emerging best practices.
• Monitor and measure workload and efficiency metrics to track progress and make ongoing improvements.
By applying the 5S methodology with a focus on reducing workload, OHS technicians can become more efficient in their roles while maintaining safety standards. This approach can lead to improved job satisfaction and better use of their time and expertise, ultimately contributing to a safer work environment.
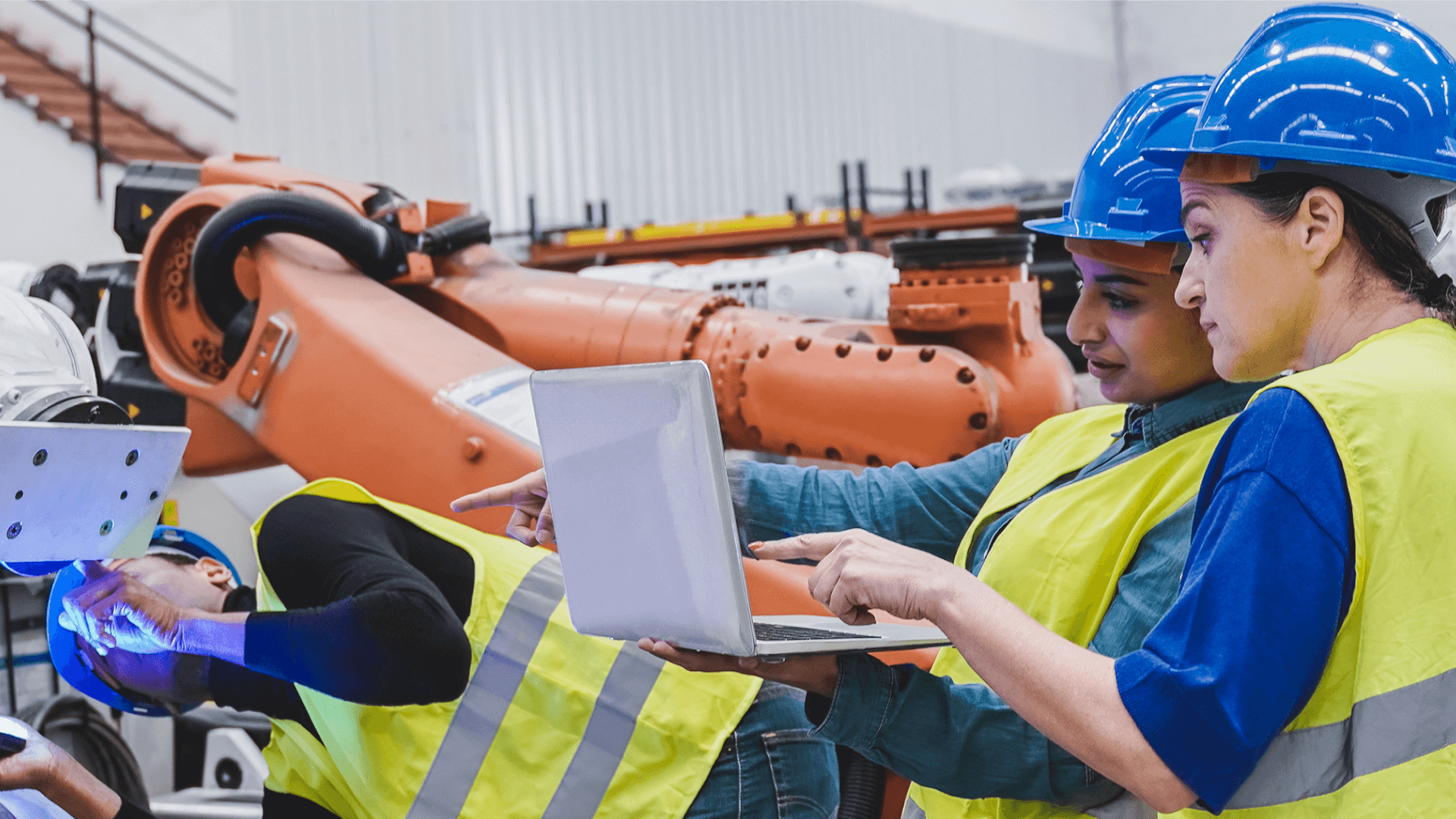
Implementing the 5S methodology in your workplace does require some initial effort, but once you establish new standards and behaviours, the benefits become self-sustaining. Consider starting with some areas in your facility to test out procedures. Measure key metrics like safety incidents, productivity, and employee satisfaction before and after implementation to demonstrate the impact of 5S on management.
Workplace safety is not just a responsibility, it is an investment in the future of our workforce and economy.
Safeguru | Delivering a Safer Future